<< Communities around the world have responded swiftly to the COVID-19 crisis with a mission to save lives and thereby, several digital solutions have been rapidly identified as useful for our current health necessities. In fact, we have seen that local manufacturing can offer a viable short-term solution for many products and components, even beyond the medical supply chain. In this article we will be looking at how online collaboration in the form of co-design and co-creation is here to help. >>
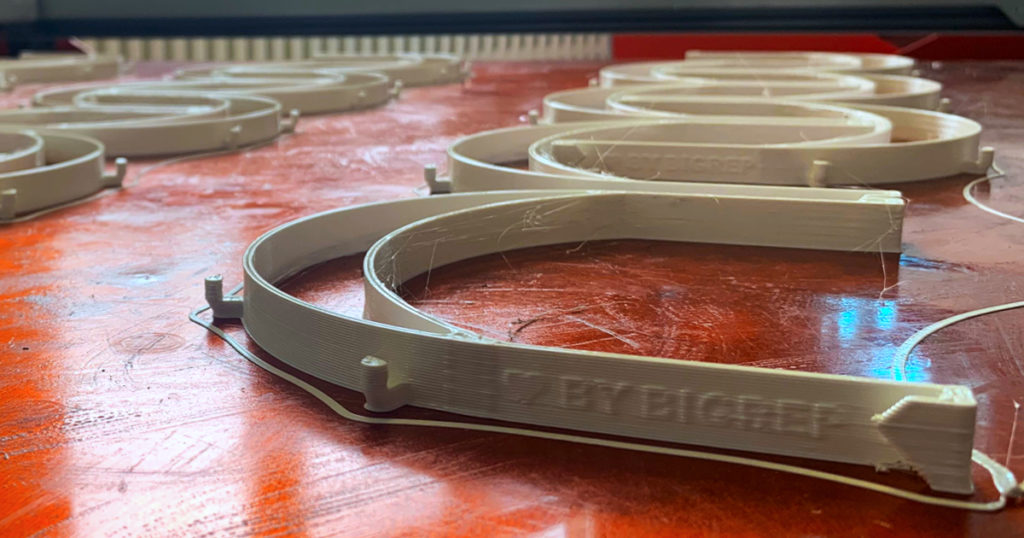
It has been an intense start of the year and one to remember: the events of recent weeks and months related to the effects of the novel coronavirus have shown us that our traditional supply chains cannot react as fast as we need them to.
This situation has shown that rather than depending on large, centralized equipment that serves only very specific cases and therefore, more flexible solutions are needed, such as distributed and agile workflows.
2020, The Year Of Online Collaboration?
Many of us have been working remotely, making active collaboration part of our new everyday life. We believe this is a good improvement - but this rapid development in digitalization, within most sectors, also highlights a critical key element as not all disciplines have successfully mastered remote collaboration: How can teams co-create when being physically separated? What tools and platforms need to be in place in order for information to flow efficiently?
We believe the most significant challenge is present in the gap between disciplines and professions as, for example, not many medical workers know how to use CAD (Computer-aided Design) Software and vice versa, not many designers or engineers have prior medical training.
How can these two fields successfully collaborate and even more, co-create? What if there could be an efficient way to collaborate between the disciplines while allowing parametric modifications “on the fly”?
Efforts in Bridging Disciplines
Before we give our take on these questions, let's start by focusing on the status quo. We’ve seen medical professionals embrace rapid prototyping and other low-cost technologies to design, fabricate, and effectively use face masks, shields, and respirator parts.
The global call of emergency has put makers and doctors together on the table - both locally and globally - to come up with quick solutions to combat this crisis together through mutual prototyping utilizing 3D-printing resulting in many, iterative designs. In this time, the accessibility and simplicity of innovative technology such as additive manufacturing can make an enormous distinction.
These Makers Turned Their Homes Into 3D Printing Factories
Makers Movement
The underlying “maker” movement and the idea of making anything, anywhere, anytime is nothing recent and has been fairly well prepared. An important figure in the movement is Professor Neil Gershenfield, who initiated the class “How to make (almost) anything” at MIT´s Center for Bits and Atoms.
In the last decade, the course has grown into an international Fabrication Academy and has spread around the globe, resulting in Fabrication Laboratories (or “FabLabs”) to pop up all around the globe. These hubs are based on enthusiasm, pragmatism, and openness towards design thinking and innovation-driven change.
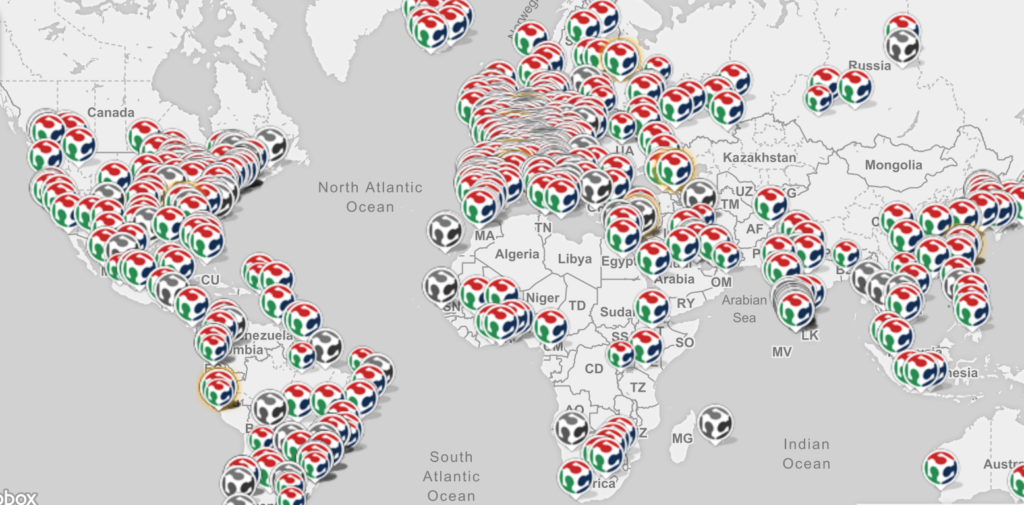
Thousands Of FabLabs Around the World
Product Configurators For Additive Manufacturing
As an example of a brand that embraces co-creation and personalization, we'd like to highly BigRep and NOWLAB. They have posted their response to COVID-19 by creating this parametric Face shield Configurator that leverages the power of additive manufacturing to tackle the supply chain challenges the world is currently experiencing.
This parametric configurator allows you to create and download a bespoke face shield, tailored to your skull and embossed with your name or brand. Moreover, if you are a BigRep client they are offering a free 2kg Filament spool for those that send them a process documentation.
“The ability to customize instantly and share 3D design ideas on demand allows us to react quickly and make adjustments when necessary, especially in times of crisis. Updates on the fly, which were previously only common in the software industry, have now become reality in additive manufacturing.” Mirek Claßen, Head of Innovation and Generative Design at BigRep.
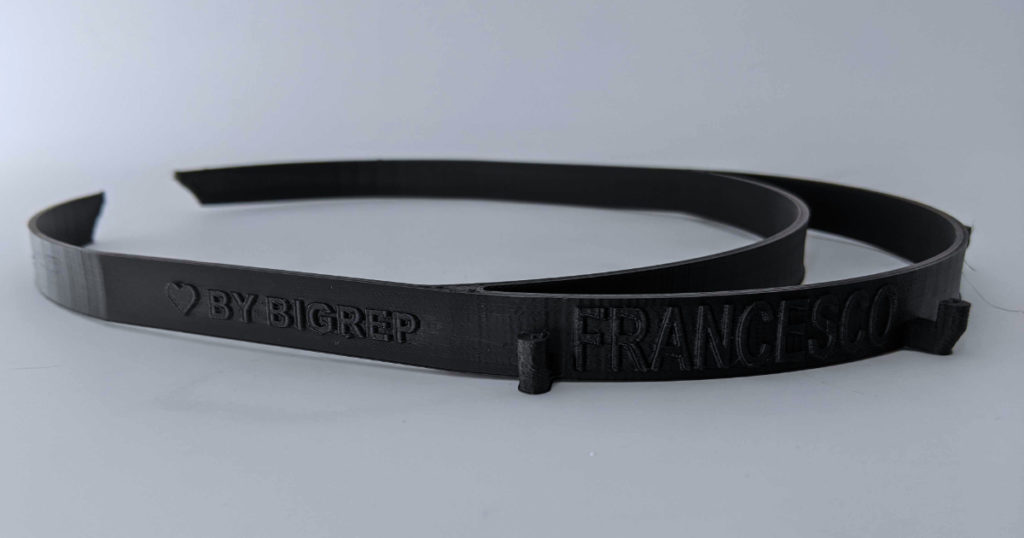
Custom Face Shield by BigRep
Additionally, we have screened and pre-selected a few prototypes that our growing user base have uploaded on our platform. These parametric models are for everyone to modify and download for free to help yourself or your community:
Other example worth highlighting include:
1. One3D has been focused on additive manufacturing and actively developed and tested a version of a face shield for dentists.
2.The Fab Lab Laba - which is part of the University of Technology in Uruguay, created project CO-INNOVACIÓN COVID-19. As part of this initiative they have been printing PPE with the help of 300(!) volunteers all over the country.
3. A Barcelona based team has started a campaign on GoFundMe to support 3D printing of emergency face shields for local hospitals to fight the virus. Big respect to all of you!
One3D Face Shields for dentists.
Can We Consider Subtractive Manufacturing?
In contrast to the previous examples which rely on additive manufacturing (a layer-based build-up of materials), we also want to bring to your attention the opposite: subtractive fabrication technique: The production of a laser-cut shield can be 200 times faster compared to 3D printing. In merely six hours, it is possible to produce more than 1000 pieces on one industrial cutting machine, thanks for the great example provided by Subdigital:
“We are used to optimize our parametric designs for efficiency. We believed there is a better way to produce the protective shields, so we started prototyping and came up with a design that takes about half a minute to produce and needs no post-production. What comes out of the laser cutter is a product ready for shipping.” Jan Pernecky, CEO of Subdigital.
Conclusions
In order to leverage the expertise of several disciplines in this crisis (and beyond), we will need platforms and configurators that allow CAD experts and non-experts to actively, parametrically and in real-time collaborate in the easiest and quickest way possible. Shapediver works robustly all around the globe, at any given time without the need for any additional software installations and steep-learning curves often involved in CAD Software.
<< Do you have a story you'd like to share with us? Reach out using our contact form at the top of this page! >>